Tunnel Construction
Preventing damage, cracks and material fracture
Engineers who have a better understanding of the wear and fracture of tools used in subterranean tunnel construction factories will be able to prolong it and render the construction of the tunnel more efficient.
Whenever a new tunnel has to be built, the building contractors face a dilemma: in order to keep the cost low, the construction should be completed as quickly as possible. However, the faster a tunnelling machine drills through soil, the greater the load on the tools and the more severe the wear. RUB engineers researching into many different aspects of tunnel construction in Collaborative Research Centre 837 help finding the perfect balance between rapid progress and non-destructive construction methods.
A moving factory works its way through the soil
Arne Röttger from the Institute for Materials focuses on tools that are deployed at the so-called working face. “What you have to bear in mind is that in tunnel construction a moving factory works its way through the soil,” as he describes the process. At the working face, the soil is excavated. The cutterhead is the front end of a tunnel boring machine with a length of up to 200 metres and a height of up to 17 metres. Depending on the condition of the soil, chisels and disc cutters are attached to the cutterhead. The chisels are used to scrape away soil, the disc cutters create stress fractures in solid rock, thus facilitating soil excavation.
Removal of the overburden and the transport of material supplies are a logistic feat.
Arne Röttger
The overburden is removed and domed segments are instantly installed in the emerging cavity; the gap between soil and the concrete segments is filled with shotcrete. “Removal of the overburden and the transport of material supplies necessary for tunnel construction that arrive from the opposite direction are a logistic feat,” says Arne Röttger.
“Depending on the composition of the soil, the tools at the open face wear out at different speeds and in different respects,” he explains. Softer metal parts, for example, are scratched or furrowed by hard components of the soil. Whereas hard materials develop cracks that expand under continuous load and may result in so-called catastrophic failure, namely the entire tool breaking. In order to prevent such brittle fracture, it is necessary to ascertain the potential presence and precise location of erratic strata in the soil. Large rocks may destroy excavation tools by a hammering load. In order to identify them in advance, engineers and geoscientists examine the building ground before tunnel construction commences.
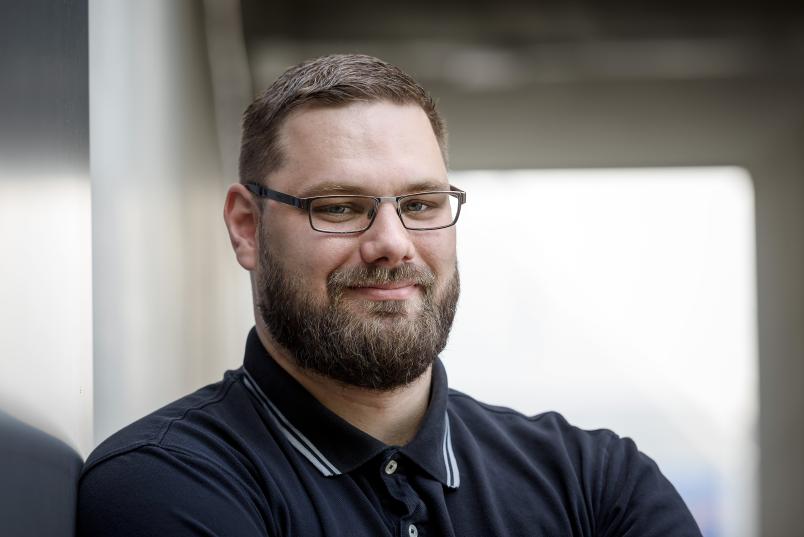
Replacing tools in the tunnel boring machine requires a lot of effort and generates high cost: the tunnelling machine has to back up, engineers have to work in the unfinished tunnel at the between the shield and the working face and this under hazardous conditions, sometimes even under excess pressure.
“This is why we try to gain a better understanding of crack initiation and propagation in such materials,” says Arne Röttger. Better understanding will lead to better prognosis of wear. “After all, you can’t see in which condition the tools are at any given moment,” explains Röttger. “Our goal is to be able to positively state after how many kilometres each excavation tool has to be replaced: they should not be replaced too early just to be on the safe side, but we should not wait for the machine to start failing to replace them, either.” In addition, the engineers are developing optimised materials for different types of loads.
Researchers refer to this interplay as tribological systems
The underlying idea is that not only does the tunnelling machine have an impact on the soil, but also vice versa; the entire process is, moreover, affected by other factors, for example the speed of the tunnelling machine, the penetration rate, the soil properties, as well as additional substances that are applied to the soil as so-called conditioning media in order to improve its quality. Researchers refer to this interplay as tribological systems. Röttger and his colleagues are developing customised materials for different types of load.
They are aiming at, for example, adjusting the composition and geometry of the materials, in order to optimise the excavation process and to minimise brittle fracture and catastrophic fracture. “Most tools for unconsolidated rock are made of compound materials,” points out Arne Röttger. “The substrate is high-strength steel. Plating is welded or brazed on locally, in order to protect the tool in places that are subject to extreme wear.” So-called hard alloys, hard compounds or cemented carbides, some of which possess properties similar to ceramics, are integrated into the tools to ensure additional wear protection.
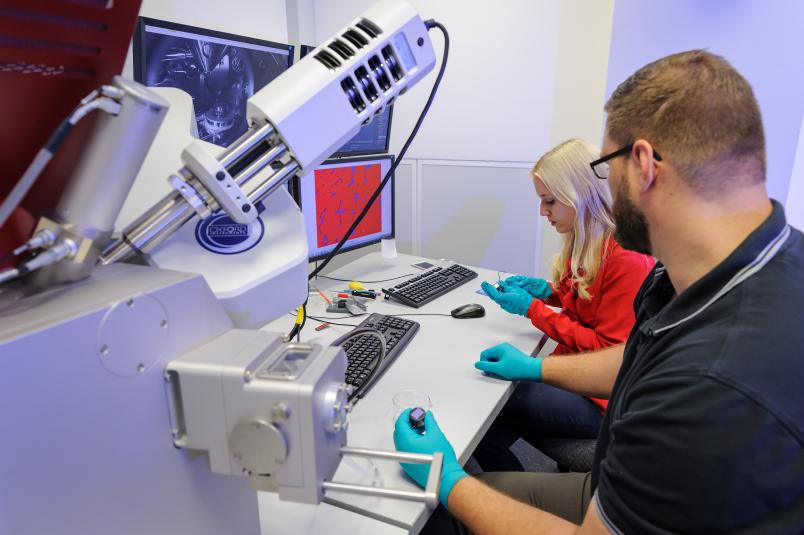
The important thing is to maintain the right balance: The harder the material, the more susceptible it is to brittle failure by cracking. Whereas softer materials may not offer the same level of resistance when carving through hard rock, but they are more tough and don’t break as easily. Moreover, the production process and thermal processing can also have an effect on material properties. “By a heat treatment, we can fine-tune the microstructure of the material and the properties associated therewith, such as material hardness and toughness,” explains Arne Röttger.
The material can be matched
In order to test different materials in experiments, the researchers run an experiment setup in the lab, where a diamond indenter scratches the material surface in question. “Using electron microscopy, we can clearly see that the diamond indenter scratches the softer metal, whereas it is lifted out of the composite structure by hard components with ceramics-like properties,” elaborates Arne Röttger.
Depending on the properties of the soil through which the machine is supposed to travel, the appropriate material is chosen, to make sure that it will resist wear over a long period of time. “Accordingly, the material can be matched to the primary wear mechanism, or in other words: it is possible to provide customised design,” concludes Röttger.