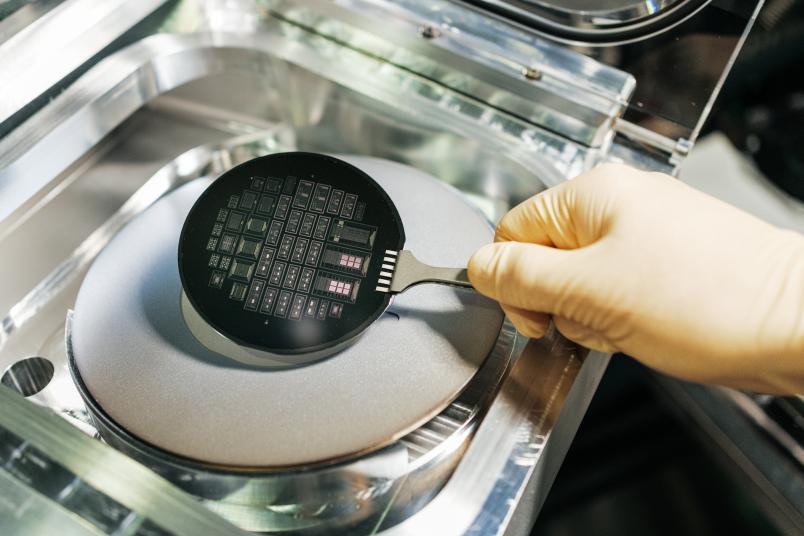
Microsystems Technology
Droplet Ballet in a Miniature Wonderland
Techniques borrowed from microchip production can be used to create tiny components. Bochum-based researchers have come up with clever tricks to set them in motion.
Four shiny spheres roll purposefully back and forth on a silvery surface. Driven by an invisible force, they tirelessly carry out synchronized movements as if performing a well-rehearsed dance. The spheres are tiny, barely visible to the naked eye, just 0.4 millimeters in size and consist of water or similar liquids. Researchers from the Chair of Microsystems Technology at Ruhr University Bochum have deposited them on a miniature silicon landscape to create a miniature moving system. What moves the droplet ballet is electrostatic force – the very same thing we play with to make bits of paper or hair stick to a balloon.
It is necessary to use electrostatic forces, as efficient electromagnetic motors are impossible to fabricate at this scale. “The smallest commercial electromagnetic motors that ever existed were two millimeters in size,” says Professor Martin Hoffmann, Head of the Chair of Microsystems Technology. Although small in a normal context, still too big to meet the requirements of his group and at the same time too inefficient to set anything in motion.
Methods from chip production
Using standard methods from microchip production, Hoffmann’s team at the Faculty of Electrical Engineering and Information Technology produces its own drives consisting of a silicon substrate and fluid spheres. By applying a voltage, the researchers ensure that an electrostatic force gets the droplets rolling.
Our aim is to use the droplets as reels to transport or precisely align tiny objects.
Martin Hoffmann
“There’s nothing special about moving the water droplets,” says Martin Hoffmann. “It has been done for a long time. Our aim is to use the droplets as reels to transport or precisely align tiny objects.” The engineers from Bochum have already shown that the principle is feasible. They created a rolling mini table by attaching a square plate to four drops of – in this case – water. “We have to apply a water-repellent layer to the underside of the plate to prevent it from getting wet,” explains Hoffmann. “Only the four corners have areas where the water adheres to the plate.” This is how the rollers are mounted on the plate.
Tiny zoom lens in the pipeline
Backed by the German Research Foundation, Hoffmann’s group now plans to refine this concept. To this end, the researchers are receiving funding from the second funding phase of the priority program “Cooperative Multistage Multistable Microactuator Systems”. One of their goals is to create a three-dimensional system in which the droplets move through a kind of high-bay warehouse. This would allow them to build a tiny zoom lens in which the droplet would act as a lens that could be deformed and moved into different positions. “But we don’t know yet if this will work,” admits Hoffmann.

In other projects, his colleagues have already successfully realized moving miniature systems – even without any water droplets. Instead, they move purpose-made silicon structures also by electrostatic force. For this to work, every detail in the construction plan is critical.
The researchers use thin silicon structures that act as ideal elastic springs. They have to carefully balance their system so that the fine structures remain stable in all conditions. Compared to other materials such as metals, silicon has one major advantage: “It doesn’t age,” says Martin Hoffmann. “If you deform a metal sheet, it might remain deformed. That doesn’t happen with silicon. It always returns to its original shape as long as you don’t stress it beyond a critical limit; then, it will break. We don’t exceed this limit, of course.”
Space-saving reflector antennas for radar systems
Bochum-based microsystems engineer Dr. Lisa Schmitt has perfected the electrostatically driven silicon springs for a system that can move a tiny mirror into a specific position. Strictly speaking, it consists of several layers and therefore also several mirrors that can be digitally controlled and moved. They direct radiation in the terahertz range into a hemisphere. Depending on how the mirrors are aligned, different radiation patterns can be generated. This could be useful for a compact, energy-efficient radar system that doesn’t require a large parabolic antenna. Such localization techniques are one of the research topics in the Collaborative Research Centre “Mobile Material Characterization and Localization by Electromagnetic Sensing” (MARIE) in which the project is embedded.
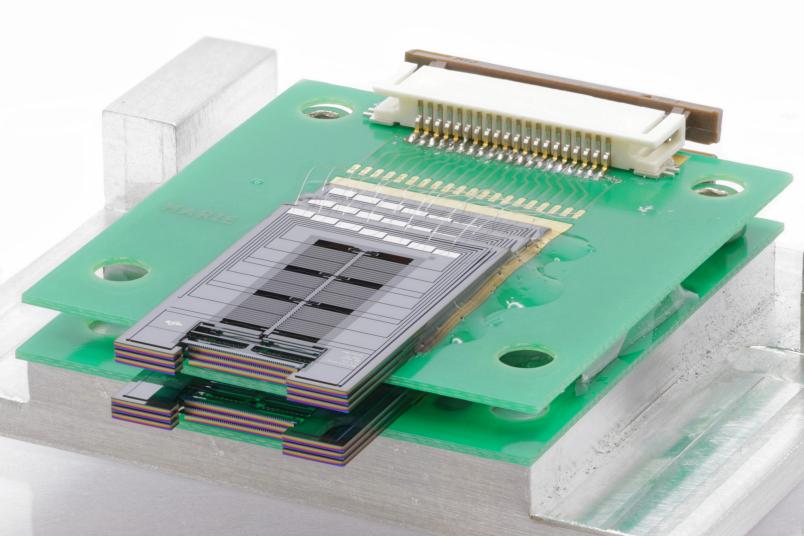
Another project that the Bochum team is tackling in collaboration with medical professionals shows just how diverse the applications for the mobile mini-systems can be. “We’ve developed a system for our colleagues that can be used to aggravate cells,” explains Hoffmann. To put it in more formal terms, the system can apply a constant force to living cells and simultaneously measure if the cell is evading or resisting.
A medical group hopes to use it to study cartilage cells that develop differently under stress – a process that is not yet completely understood. Just like the movable mirrors for radar systems, the cell aggravator consists of fine silicon structures that are moved by electrostatic force. At its heart are novel zigzag structures that act as sophisticated springs while exerting a constant force even when the cell presses against them.
Movable structures created through etching
Developing this kind of specialized component can be extremely challenging. For one thing, the mechanics have to be worked out down to the last detail, and for another, the tiny structures have to be produced with precision. They are created from large silicon blanks, so-called wafers, from which material is removed using dedicated plasma processes. The parts that are not required simply drop of the wafer during the etching process, leaving behind the required structures. “It goes without saying that we must ensure that the incorrect parts don’t drop out,” stresses Martin Hoffmann. A dance on the razor’s edge. After all, some of the structures within the springs are just two micrometers thin, i.e. two thousandths of a millimeter.
Despite all such challenges, the production of microsystems also has advantages compared to the macroscopic world: “We don’t have to assemble anything,” says Hoffmann. The system leaves the etching process complete including all the necessary connections. “And once a structure has been designed, we can reproduce it millions of times,” says the Bochum-based researcher.
What’s more, the fully developed components, such as the specialized springs described above, can also be used for other applications. Once an element has been tried and tested, it will also be applied in other systems, and the researchers don’t have to start from scratch every time. Hoffmann’s team still has plenty of ideas for new applications and systems. In the future, many water droplets will continue to dance across surfaces in the Bochum labs as if by magic and miniature springs will continue to do their job.