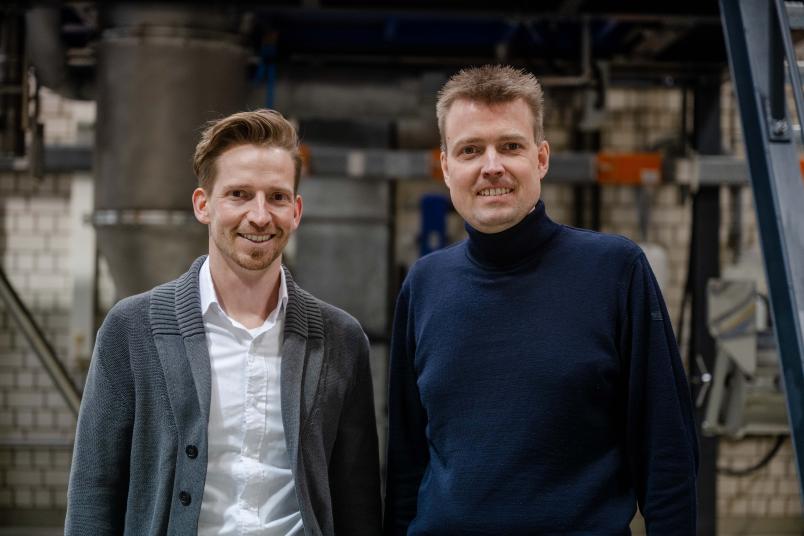
Materials research
Making metal 3D printing more efficient
The potential for energy and material savings offered by additive manufacturing compared to conventional processes is enormous. But the devil is in the details.
Metal components can not only be designed more flexibly using 3D printing. So-called additive manufacturing also saves material and energy compared to conventional manufacturing processes such as casting of a melt. The aim of the REACT project, short for “Resource Efficient Additive manufacturing of martensitic Cr-sTeels”, is to fully exploit these savings potentials. The project, led by Professor Sebastian Weber, holder of the Chair of Materials Technology at Ruhr University Bochum, Germany, will start with a kick-off event for all six partners on 14 March 2023. It is funded with 1.7 million euros by the Federal Ministry for Economic Affairs and Climate Protection.
Saving raw materials
Additive manufacturing comprises various processes, each of which only puts the material where it is supposed to remain. One example is powder bed-based 3D printing with metal powders. In this process, a thin layer of powder is spreaded onto a building platform and the powder particles are then melted with a laser beam and bonded together only where the finished component is created. Layer by layer, the product is formed in the powder bed. The loose powder is removed later, only the component remains. However, there is still a lot of research to be done around this process: How, for example, can we succeed in producing powder particles that are all the optimum size for additive manufacturing? “Particles that are too large or too small have to be discarded”, explains Sebastian Weber. “That’s why we calculate in advance of powder production how we can optimise the yield of suitable particles as much as possible.” A laboratory-scale powder atomisation plant is available for experiments.
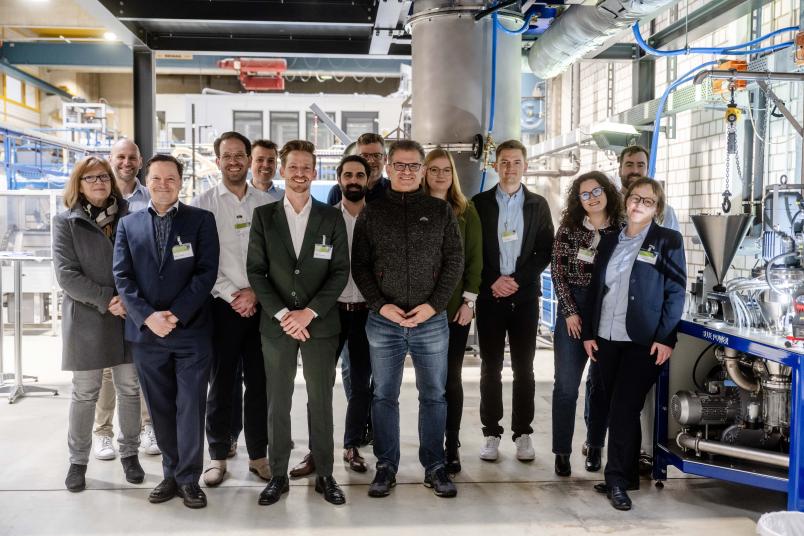
Improving material properties
The composition of the material, in this case martensitic chromium steel, is also the subject of research. “Tried and tested alloys were developed for other applications, such as casting processes, and repurposed for additive manufacturing”, explains research group leader Dr. Jonathan Lentz. “The recipes of the alloys have to be adapted for additive manufacturing processes.” The researchers from Bochum are focusing their attention primarily on the element nitrogen as an alloy component. Used correctly, it can increase the printability and durability of additively manufactured components. However, you have to keep an eye on nitrogen during all process steps, as it tends to outgas”, says Sebastian Weber.
Recycling everything
Last but not least, the partners in the project are also addressing the question of how additively manufactured metal products and leftover powders can be recycled or upcycled for 3D printing to create a closed loop. “A preliminary analysis has shown that the new manufacturing strategies offer the potential to save up to 97 percent of energy in the focused products of the project partners – and that with faster and cheaper production with better material properties”, Weber summarises.
Optimising the entire process chain
The project consortium will map the entire process chain from the production of the steel to the refinement of the end product. This makes it possible to view and optimise the process chain holistically. The Chair of Materials Technology accompanies all steps from the development of alloys to the production of metal powders, 3D printing and heat treatment to the characterisation of the final products. Special focus is placed on balancing energy efficiency along the process chain.