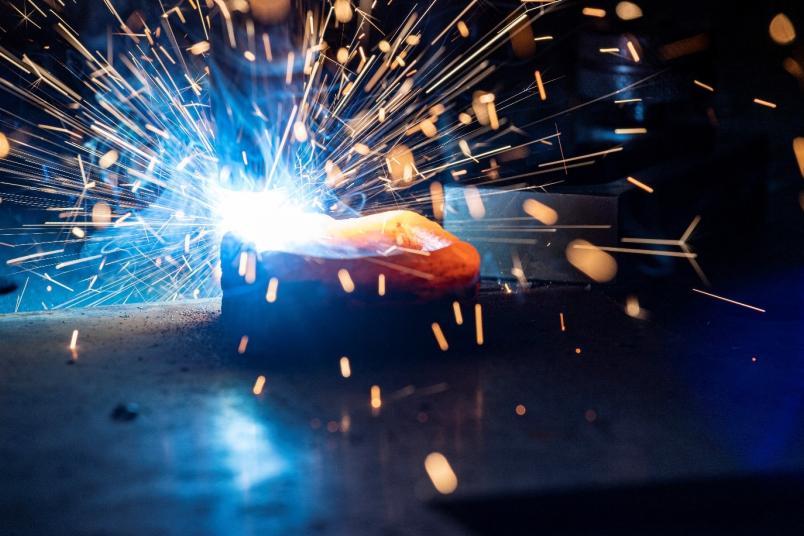
Materials research
Powder-filled wires for highly customizable alloys
A new project aims to aid the fast and efficient production of customised steel workpieces.
Some workpieces can’t be successfully manufactured using conventional methods such as casting. In such cases, the obvious choice is to use an additive manufacturing process. Optimising this process is the goal of the EWA project, which stands for the “development of carbon-martensitic tool steels for the additive manufacturing of highly stressed forming tools using wire-arc additive manufacturing”. The starting materials for this additive manufacturing process are thin, powder-filled wires. They are additively processed into punching and forming tools. The project at the Chair of Materials Technology at Ruhr University Bochum, Germany, headed by Professor Sebastian Weber, is funded by the Central Innovation Programme SMEs of the Federal Ministry of Economics and Energy. It will start with a kick-off event on 22 June 2023.
Welding without rotary swaging and wire drawing
The so-called wire-arc additive manufacturing (WAAM) is largely based on gas metal arc welding (GMAW). The starting materials are inexpensive metal wires. The EWA project utilises so-called metal-cored wires: tubes filled with metal powder with an outer diameter of at least 1.2 millimetres. “These cored wires allow a high degree of flexibility in the alloy composition, which is produced directly in the cored wire,” explains Ulf Ziesing from the project team at Ruhr University Bochum. “Due to the powder filling, which liquefies directly during welding, there’s no need to first produce a melt that would have to be reduced to the required wire diameter by means of rotary swaging and subsequent wire drawing.” While it’s often not possible to draw hard-phase-rich and high-strength materials to the small diameters of the wires, they can be produced as cored-wires.
When using the WAAM process, the material is applied according to an underlying 3D CAD model only in those areas where it is required. This means that 90 to 100 per cent of the material applied in the process can be effectively retained all the way to the finished workpiece. “This high degree of utilisation translates into significant material savings and, consequently, an improved CO2 footprint compared to the conventional, casting-based processing route,” points out Ulf Ziesing. Moreover, the molten material cools down quickly during GMAW, resulting in a state of high solution. All this renders the mechanical properties of a workpiece produced by WAAM superior to those of a conventionally produced component.
Plus, it’s a high-speed process: up to twelve kilogrammes of material can be applied within one hour. “All in all, this method has great potential for the production of individualised single components and complex small series in large format,” concludes Ulf Ziesing.