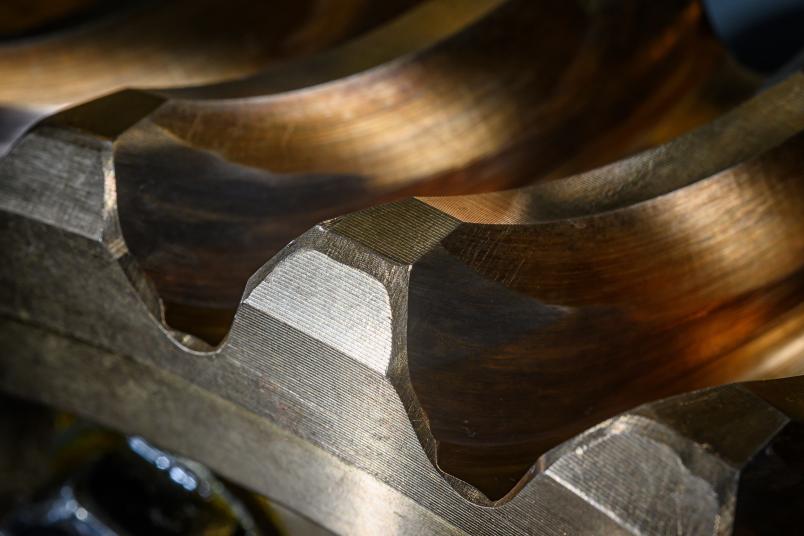
Drive Technology
Blank Teeth Make for Smooth Running
Gear wheels should be able to interlock smoothly. Manufacturers come up with various tricks to make sure that they do. Researchers in Bochum have found out just how effective they are.
Gear wheels usually do their job in the background. But without them, everything comes to a standstill: There’s no car, no airplane, no dentist’s drill, no wind turbine. As they are deployed on a massive scale, it’s worth investing in quality and, as a result, in both the service life of the machines they drive and the energy efficiency of the relevant processes. Professor Manuel Oehler’s team from the Chair of Drive Technology at Ruhr University Bochum, Germany, provide an overview of where the levers are and which measures are most effective. Rubin, the science magazine of Ruhr University Bochum, features an article on their research.
The employees at the Chair of Drive Technology determine how durable the gears actually are on their test benches, which fit gears of many different sizes. The running times range from a few minutes to several days, and the rotational speeds can also be adjusted. Jaacob Vorgerd uses pieces of gearwheels that have undergone these tests to show what happens over time: First, the surfaces of the teeth on the flank with which they are in contact with the paired gear are worn down. Initial wear is barely visible to the naked eye. More pronounced wear and tear is caused by friction and heat.
Does surface finishing pay off?
To ensure that even minor signs of wear can be delayed for as long as possible, the tooth surfaces that come into contact with each other are key. The smoother the surface, the less friction and wear typically occur in operation. The team at the Chair has investigated the effects of various additional surface finishes, such as vibratory grinding and shot peening of the gear base.
The costs for these finishing techniques account for 10 to 15 percent of the total cost of a gear. Is it worth the effort? This is the question industrial partners put to the Chair. The answer is a resounding yes. “If the efficiency increases by just one percentage point as a result of such a treatment – for example from 98 to 99 percent – this means that the power loss is halved,” points out Manuel Oehler. “99 percent of the energy that drives the gear is transferred to the desired movement of the drive, and only one percent dissipates in the form of heat.”
Detailed article in science magazine Rubin