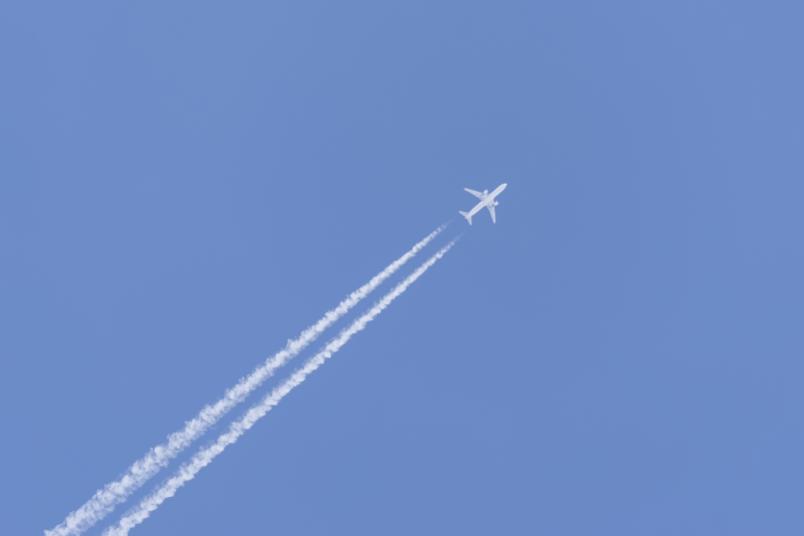
Mechanical Engineering Flying with a Clearer Conscience
Researchers are modeling a virtual aircraft engine. Their aim is to pave the way for more sustainability in air travel.
Air passenger numbers have recovered noticeably after the Covid pandemic: In its monthly statistics, the EU Commission reports a 56 percent increase in the number of air passengers compared to the first quarter of 2022, with 179 million passengers in the first quarter of 2023. The International Air Transport Association (IATA) expects global air traffic to increase by 103 percent compared to 2019. However, many passengers are likely to board the plane with a guilty conscience. This is because flying consumes fossil fuels and causes greenhouse gas emissions. “We have to step up our research efforts in order to make flying more eco-friendly,” says Professor Francesca di Mare.
As the holder of the Chair of Thermal Turbomachinery and Aero Engines at the Faculty of Mechanical Engineering at Ruhr University Bochum, she launched an ambitious EU project called MYTHOS in early 2023. MYTHOS is an acronym for “Medium-range hybrid low-pollution flexi-fuel/hydrogen sustainable engine”. Research institutions from three European countries are involved in the project.
Engine design affects fuel consumption
The project aims to establish fundamental insights, based on which sophisticated design methods can be developed to facilitate the flexible use of various sustainable aviation fuels (SAF), including pure hydrogen, in engines. To this end, the consortium, headed by Francesca di Mare, will design a detailed virtual model of a complete engine that can be used to accurately calculate how the engine behaves during all phases of a flight – from start, through take-off, flight and landing.
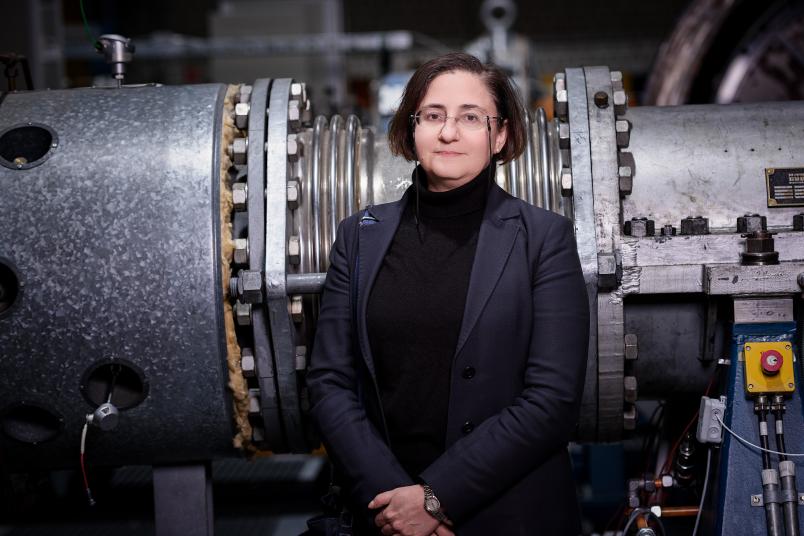
“The processes in the engine are very complex and operating conditions change during the flight,” explains Francesca di Mare. “How the individual components are designed greatly affects the efficiency of the entire engine and hence the fuel consumption. In this respect, the combustion chamber is of particular importance: The fuel must be used as efficiently as possible so that the turbine can generate the necessary power.” To give an example: ”When taking off with a full load, an A380 aircraft requires the power of around 400 Formula 1 cars – one such vehicle has around 800 hp. A suboptimal design of the combustion chamber and the entire engine leads to increased fuel consumption and therefore automatically to increased emissions,” as Francesca di Mare illustrates the problem.
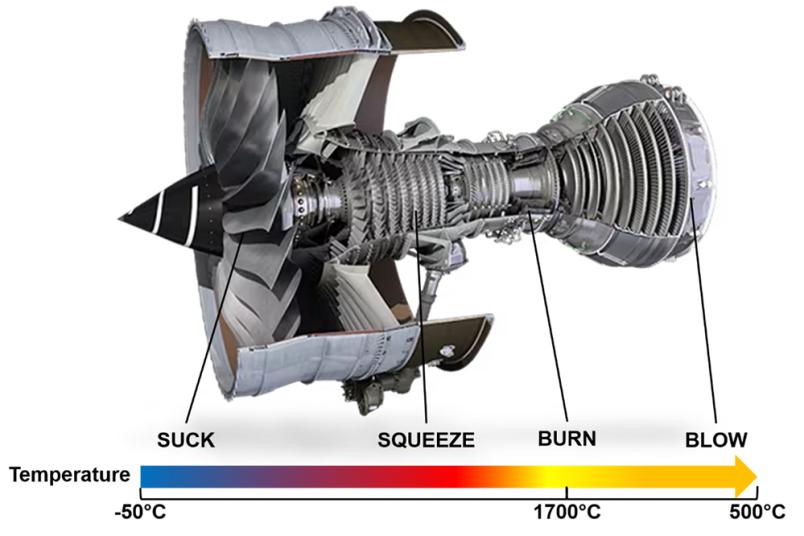
The working principle of an aircraft engine follows the “suck-squeeze-burn-blow” sequence: The amount of energy in the air is increased by compression and supply of chemical energy bound in the fuel in the combustion chamber, being finally released in the turbine to generate thrust.
How do pressure and temperature build up at each individual point?
The virtual model created for the project will include every component of the engine, allowing a highly accurate calculation of how even minor adjustments affect the entire system. How does the flame spread and stabilize in the combustion chamber? How does the air flow past the individual turbine blades? How much load is placed on the individual parts? How do pressure and temperature build up at each point in the engine?
“We model these processes down to the smallest detail and use machine learning to identify how they are connected,” explains the researcher. “We’ll then reduce the model complexity to ensure that it remains manageable and can be applied without too much effort while still achieving maximum accuracy.” The consortium intends to make the entire engine model available to the research community.
Large-scale production of Sustainable Aviation Fuels remains problematic.
Francesca di Mare
At the same time, the team plans to carry out calculations for three representative fuels that could be used in aviation in the future: These belong to the class of the so-called SAFs, Sustainable Aviation Fuels, which can be produced from various sources, for example from plant products, recycled waste oils and synthesization processes. “The problem with SAFs, which are already being used to some extent today, is that there isn’t enough of them,” points out Francesca di Mare. “Fuels made from plant-based raw materials in particular have a very low energy density and are therefore hardly an economically viable solution. In addition, there are ethical concerns about the use of agricultural land, as outlined in the CORSIA guidelines and definitions.” CORSIA stands for Carbon Offsetting and Reduction Scheme for International Aviation.
The research team therefore includes synthetic kerosene, recycled used oils and hydrogen in its calculations. “Unfortunately, there isn’t enough hydrogen, either,” says di Mare. “And we still face considerable technological problems that need to be solved in order to enable large-scale use in aviation.”
Hydrogen is characterized by its high volatility (it diffuses about four times faster than methane or vaporized kerosene in air, for example) and very low density. In order to exploit its high energy density by mass – it contains 142 megajoules per kilogram compared to 43 megajoules per kilogram for kerosene – hydrogen would have to be highly compressed. “To force 1 kilogram of hydrogen into a volume of 1 cubic meter, we’d need a pressure of around 1,000,000 pascals at an ambient temperature of 25 degrees Celsius,” explains Francesca di Mare. “Or we’d even have to liquefy it – at a temperature of below minus 200 degrees Celsius and a pressure of 7,000 pascals. Cryogenic combustion, which uses liquid hydrogen, is common in rocket engines, for example,” continues the researcher. These properties present an enormous challenge for the design of engines and aircraft, simply because of the necessary cooling infrastructure and storage space, and this is precisely what the researchers in the MYTHOS consortium will be addressing.
An adaptable model
“It will therefore still be quite a few years before commercial flights with hydrogen will take off; still, this revolutionary transition in aviation is one of the main pillars of the European climate law ‘FitFor55’ and the strategic agenda of the European Clean Aviation Partnership. Our research contribution is therefore more necessary than ever,” concludes Francesca di Mare. Di Mare’s team is striving to demonstrate the methodology and thus lay the groundwork that will ultimately pave the way for future technological developments.