Drive Technology Blank Teeth Make for Smooth Running
Gear wheels should be able to run smoothly. Manufacturers come up with various tricks to make sure that they do. Researchers in Bochum have found out just how effective they are.
Gear wheels usually do their job in the background. But without them, everything comes to a standstill: There’s no car, no airplane, no dentist’s drill, no wind turbine. “Every standard car has at least 15 gear wheels installed between the engine and the wheels. In a battery-powered electric vehicle, the number is usually only half as many, but even here nothing would move without gears,” as Professor Manuel Oehler illustrates the sheer mass of the components. And that’s not even counting the parts needed for electric windows, wing mirrors, seat adjustment mechanisms and other ancillary functions. And cars, with their comparatively few operating hours, are just one example of how gear wheels are used on a massive scale. It’s therefore worth investing in the quality of gears and, as a result, in both the service life of the machines they drive and the energy efficiency of the relevant processes.
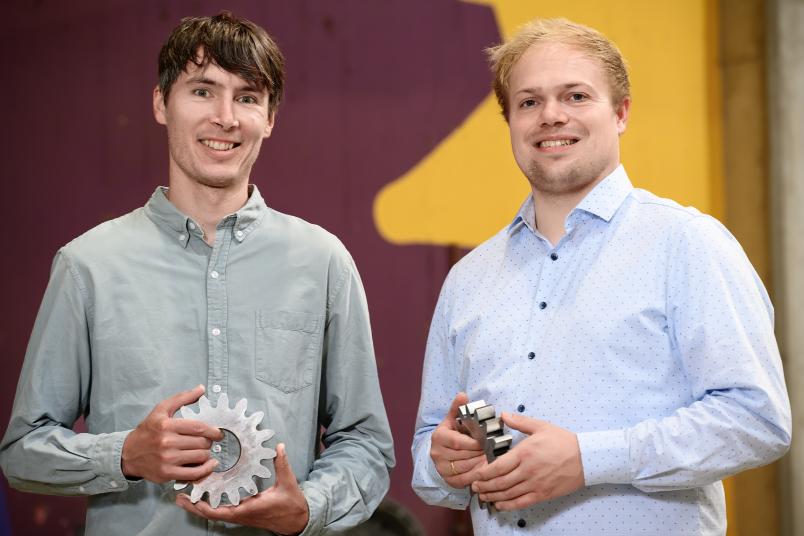
The team at Oehler’s Chair of Drive Technology at Ruhr University Bochum, Germany, is currently exploring which adjustments can be made to ensure that a gear runs smoothly for a long time. The engineers also hope to find out whether and how damage to gears can be predicted so that maintenance respectively replacement intervals can be planned effectively. “Picture an offshore wind turbine: You can tell just how much effort it takes to replace a gearwheel in its gearbox,” explains Dr. Jaacob Vorgerd, senior engineer at the department. Considering that this requires special ships and cranes, it makes sense to know exactly when the intervention is really necessary.
High-grade steels, slimmer gears
At the Chair, the life of a gear wheel can be tracked practically from start to finish. “Our students manufacture the gears in our workshop and measure them with micrometer precision – whereas we source them from project partners for all other purposes,” explains Manuel Oehler, pointing to an antique-looking green milling machine. The vast majority of gear wheels are made of steel. The individual teeth are milled out of a round blank. The students have the opportunity to try all these steps out in the workshop. In industrial production, the process is automated and the gears then undergo heat treatment to harden the surfaces. A final grinding process makes the wheel ready for use.
In applications that require exceptional performance – such as aircraft construction or wind turbines – the effort involved is often greater. “In aircraft construction, safety is of course of paramount importance,” says Manuel Oehler. By choosing high-grade steels, it’s possible to design slimmer gears without any loss of function. This reduces weight.
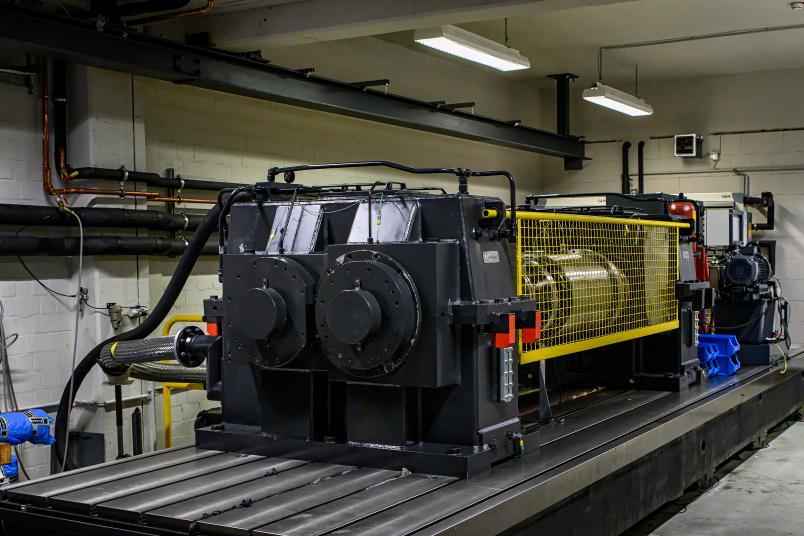
The employees at the Chair of Drive Technology determine how durable the gears actually are on their test benches, which fit gears of many different sizes. The running times range from a few minutes to several days, and the rotational speeds can also be adjusted. Jaacob Vorgerd uses pieces of gear wheels that have undergone these tests to show what happens over time: First, the surfaces of the teeth on the flank with which they are in contact with the paired gear are worn down. Initial wear is barely visible to the naked eye. More pronounced wear and tear is caused by friction and heat. “In the worst case, the teeth become discolored and deformed. Individual teeth may even break off,” as Vorgerd demonstrates on a component of a helicopter gearbox that was run without oil for test purposes until it failed. “Our intention was to show that the helicopter could still land safely even in the event of total failure,” he explains.
To ensure that even minor signs of wear can be delayed for as long as possible, the tooth surfaces that come into contact with each other are key. The smoother the surface, the less friction and wear typically occur in operation. The team at the Chair has investigated the effects of various additional surface finishes: In vibratory grinding, the gears are immersed in a basin with ceramic bodies, which are made to vibrate and remove tiny particles from the already ground surface. “It’s like a river pebble that becomes smoother and smoother the longer it lies in water,” illustrates Manuel Oehler. Measurements with an autofocus microscope, which can record surfaces including height information, have shown that this reduces the roughness of the surface to elevations of 0.1 micrometres – after standard grinding it’s 0.3 micrometres. Just like sandblasting, the steel surface is bombarded with tiny metal beads. This creates tiny indentations that harden the surface. “This increases resistance to the finest cracks,” explains Jaacob Vorgerd.
The costs for these finishing techniques account for 10 to 15 percent of the total cost of a gear. Is it worth it? This is the question industrial partners put to the Chair. The answer is a resounding yes. “If the efficiency increases by just one percentage point as a result of such a treatment – for example from 98 to 99 percent – this means that the power loss is halved,” points out Manuel Oehler. “99 percent of the energy that drives the gear is transferred to the desired movement of the drive, and only one percent dissipates in the form of heat.”
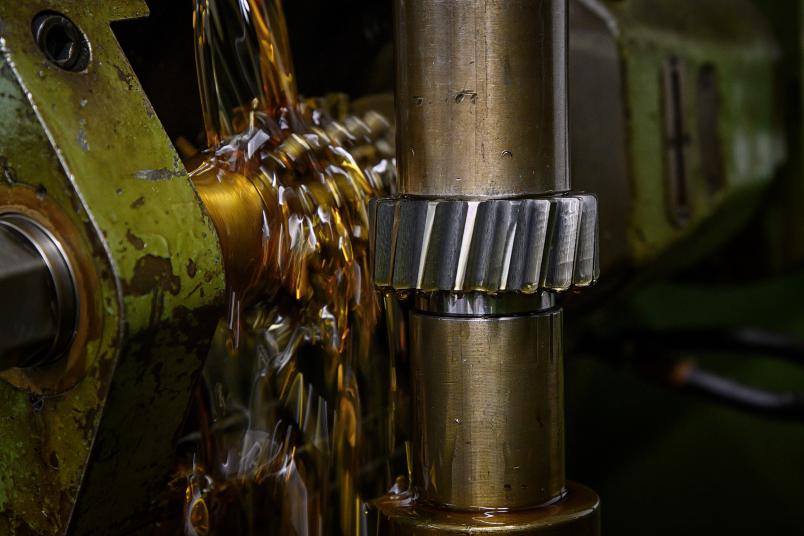
Simulation of damages
The effects can be measured on the Chair’s test benches. “By measuring vibrations in particular, we can tell how smoothly a gearwheel is running,” explains Jaacob Vorgerd. “Stronger vibrations are a sign of damage, for example very fine cracks in the surfaces.” Another indicator is the temperature of the lubricant in question: Comparing the temperature of the oil that lubricates the drive when it enters and when it leaves is a highly accurate method of measuring friction.
In line with these experiments, the researchers are developing models to simulate damage to gears. This is how they try to predict how long a gear wheel will run without problems, how long a maintenance interval should be and when the part should be replaced as a precaution.