Neues Messgerät
Sonde misst die Plasmadichte
Plasmen sind ein Bestandteil vieler industrieller Prozesse, zum Beispiel bei der Beschichtung von Oberflächen. Um sie möglichst effizient einzusetzen, muss die Plasmadichte bekannt sein.
Effizient mit Ressourcen zu haushalten ist eine Jahrhundertaufgabe. Eine erfolgversprechende Strategie basiert auf der Oberflächentechnik. Warum ein ganzes Bauteil aus teuren Materialien herstellen, wenn es nur auf die funktionale Oberfläche ankommt?
Um Benzin zu sparen, hat die Autoindustrie schwere Metallspiegel durch leichte metallbeschichtete Kunststoffteile ersetzt. Brillengläser bestehen ebenfalls aus Kunststoff, was einen hohen Tragekomfort gewährleistet; eine harte dünne Schicht auf der Oberfläche schützt sie vor Kratzern. Auch die Hi-Tech-Industrie hat die dünnen Schichten entdeckt: Optische Filter zum Beispiel erhalten durch die Technik ihre Fähigkeit, nur bestimmte Lichtwellenlängen durchzulassen.
Eines der Werkzeuge der Oberflächentechnik beruht auf Plasmen. Ein Blick auf die verwendeten Prozesse verrät den Grund: Um Brillengläser oder optische Filter zu behandeln, kommt die plasma ion assisted deposition, kurz PIAD, zum Einsatz. Der Prozess läuft in einer Vakuumkammer von einem Meter Durchmesser ab.
Die zu beschichtenden Gegenstände hängen an der Decke. In einem Tiegel am Boden befindet sich das Material, das die weniger als einen Mikrometer messende Schicht auf der Oberfläche bilden soll, zum Beispiel Titanoxid. Durch Elektronenstrahlen wird es verdampft, verteilt sich gleichmäßig in der Kammer und lässt sich auf den Gläsern nieder. „Das Dumme ist, dass das verdampfte Material selbst nicht viel Energie hat“, erklärt Prof. Dr. Ralf Peter Brinkmann vom Lehrstuhl für Theoretische Elektrotechnik. „Die Teilchen setzen sich dort, wo sie ankommen, auf die Oberfläche. Und das ergibt eine ungeordnete, ganz lockere Schicht.“
Die plasmatechnische Variante einer Dampframme
Damit die Schicht robust ist und die richtigen optischen Eigenschaften bekommt, sollten die Teilchen jedoch dicht gepackt sein. Hier kommt das Plasma ins Spiel. Es wird von einer eigenen Quelle als Plasmastrahl ausgesendet und liefert die notwendige Energie, die den Schichtteilchen selbst fehlt. Die energiereichen Plasmateilchen (Ionen) treffen gleichzeitig mit den Schichtteilchen auf die Oberfläche und sorgen dafür, dass die Schicht eine kompakte Form annimmt. „Wenn man so will, die plasmatechnische Variante einer Dampframme“, vergleicht Brinkmann.
Ein Plasma charakterisieren
Mit dem technischen Fortschritt werden die Anforderungen an die aufgetragenen Schichten immer größer; immer präziser müssen diese gefertigt sein. Wichtig sind dabei zum Beispiel eine gleichmäßige Dicke der Schichten und gleichmäßige optische Eigenschaften.
Im Projekt „Pluto: Plasma und optische Technologien“ haben sich wissenschaftliche Institute und Firmen gemeinsam dieser Herausforderung gestellt. Das Bundesministerium für Bildung und Forschung (BMBF) förderte sie von Mai 2009 an fünf Jahre lang.
Die RUB-Ingenieure konzentrierten sich dabei auf das Plasma und eine geeignete Diagnostik zu dessen Charakterisierung. Um es während der Beschichtung stabil zu halten, muss man seine Eigenschaften kennen, es also während des laufenden Prozesses vermessen.
„Das ist ein Problem“, erklärt Ralf Peter Brinkmann. „Denn leider werden nicht nur die eingebrachten Brillengläser oder optischen Filter beschichtet, sondern ausnahmslos alle Oberflächen.“ Auch auf den Messinstrumenten wachsen somit dünne Schichten – für das bisherige Standardmessverfahren, die Langmuir-Sonde, untragbar.
Alternatives Messprinzip ausgedacht
Also ließ sich der Bochumer Forscher mit seinen Doktoranden ein alternatives Messprinzip einfallen. Es basiert auf der Tatsache, dass Plasmen schwingen können: Die freien Elektronen im Plasma bewegen sich in eine Richtung, bauen dabei ein elektrisches Feld auf, das sie schließlich stoppt und dann in die andere Richtung beschleunigt. Dabei bauen sie erneut ein elektrisches Feld auf, das aber dem ersten entgegengesetzt ist. Auch dieses Feld stoppt die Elektronen, und beschleunigt sie dann wieder in die ursprüngliche Richtung. Der Prozess wiederholt sich mit einer regelmäßigen Frequenz. Über die Frequenz dieser Schwingung – sie liegt etwa zwischen 100 Megahertz und 10 Gigahertz – lässt sich die Elektronendichte bestimmen.
Um die Frequenz zu messen, entwickelte Brinkmanns Team in Zusammenarbeit mit drei weiteren Lehrstühlen der RUB im Projekt Pluto die Multipol-Resonanz-Sonde. Diese wird an geeigneter Stelle im Plasma positioniert und sendet ein hochfrequentes elektromagnetisches Signal aus, genauer eine Sequenz kurzer Impulse. Das Plasma reagiert auf diese Impulse mit seinen charakteristischen Schwingungen, die die Sonde wieder aufnimmt. Dieses Phänomen heißt Resonanz.
„Es ist, als würde man mit einem Klöppel auf eine Glocke schlagen“, veranschaulicht Prof. Brinkmann. Der Schlag mit dem Klöppel entspricht dem Impuls; die Glocke reagiert mit ihrer charakteristischen Schwingung. „Der gleiche Schlag bei einer anderen Glocke würde einen anderen Ton ergeben“, so der Forscher.
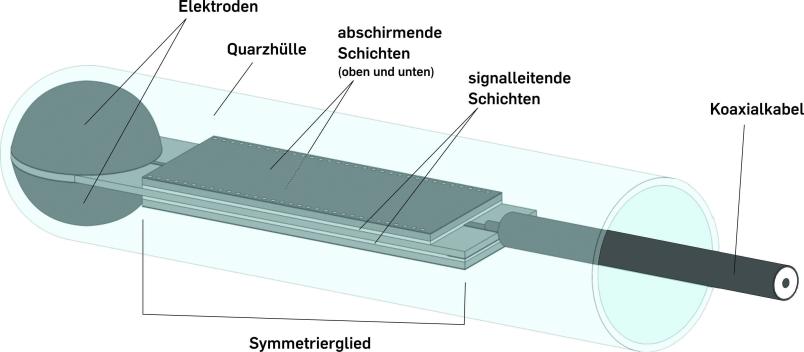
Aus der charakteristischen Schwingung lässt sich über ein mathematisches Modell die Elektronendichte ausrechnen. Klingt einfach. Ganz so leicht ist es aber nicht. „Wir haben unsere Sonde von vorneherein so designt, dass sich die Berechnungen am Ende mit einer einfachen Formel machen lassen“, erklärt Brinkmann. „Sie ist erstaunlich einfach. Wenn wir die Sonde nicht speziell so gebaut hätten, dass diese Formel zutrifft, könnte in mathematischer Hinsicht beliebig viel Kompliziertes passieren.“ Schlüssel zum Erfolg ist die Symmetrie des Messinstruments. Sie erlaubt die Anwendung der sogenannten Multipol-Entwicklung.
Nicht nur auf mathematischer Ebene galt es, einige Hürden zu überwinden. Die Multipol-Resonanz-Sonde benötigt auch eine spezielle Elektronik, die der Lehrstuhl für Elektronische Schaltungstechnik von Prof. Dr. Thomas Musch entwarf und baute. Sie liefert hochstabile Signale, die die Sonde braucht, und kann die zurückkommenden Signale aus dem Plasma präzise interpretieren.
„Dafür gibt es natürlich schon Labormessgeräte zu kaufen, die sogenannten Netzwerkanalysatoren“, erzählt Ralf Peter Brinkmann. „Aber die sind groß, teuer und nicht robust genug für den Einsatz in industriellen Prozessen. Wir wollten zu einem kleinen Kasten kommen, der preiswert ist und unter den harten Einsatzbedingungen über viele Jahre zuverlässig arbeitet. Und das gelang unseren Kollegen auch.“
Der letzte theoretische Schritt, der notwendig war, um die Sonde zu realisieren, bestand in der Optimierung der Sondeneigenschaften mittels 3D-elektromagnetischer Simulationen, durchgeführt durch den Lehrstuhl für Hochfrequenzsysteme von Prof. Dr. Ilona Rolfes.
Sonde hat Tests mit Bravour bestanden
Mittlerweile liegt die Multipol-Resonanz-Sonde als Demonstrator vor, der nächste Schritt wäre ein Prototyp. Der Lehrstuhl für Allgemeine Elektrotechnik und Plasmatechnik von Prof. Dr. Peter Awakowicz hat das Messinstrument inzwischen einer Reihe von Tests unterzogen, die es mit Bravour bestanden hat.
Die Sonde misst die Plasmadichte genauso präzise wie die herkömmliche Langmuir-Sonde, liefert im Gegensatz zu dieser aber auch bei laufender Beschichtung konstant korrekte Messergebnisse. „Ich will die Langmuir-Sonde natürlich nicht schlechtmachen“, sagt Ralf Peter Brinkmann. „In den Anwendungsbereichen, in denen sie funktioniert, ist sie unverzichtbar. Die beiden Sonden sind für unterschiedliche Einsatzzwecke optimal.“
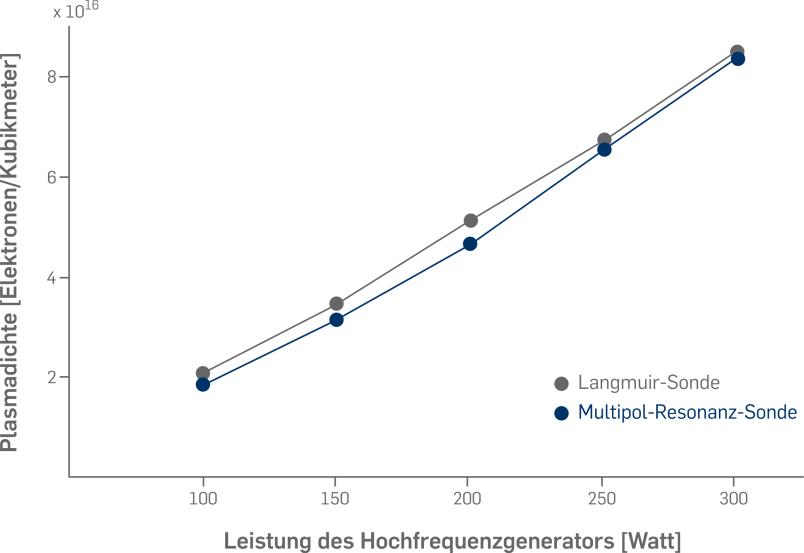
Die Bochumer Ingenieure haben deutsche und internationale Patente auf ihre Sonde angemeldet. Einige große Firmen haben bereits Interesse bekundet oder sie sogar für eigene Forschungsprojekte eingeplant.
Wenn aus dem Lehrstuhl für Theoretische Elektrotechnik am Ende etwas Praktisches herauskommt, finde ich das schön.
Ralf Peter Brinkmann
Das RUB-Team will das Messinstrument nun für den Produktionsalltag in der Industrie optimieren und beteiligt sich im BMBF-Nachfolgeprojekt „Pluto plus”. Für sehr kleine Plasmen soll auch eine Miniversion in Stecknadelgröße entstehen; bislang hat die Sonde etwa den Durchmesser eines Kugelschreibers.
Von der ersten Idee bis zum Demonstrator sind etwa sieben Jahre vergangen, auf die Ralf Peter Brinkmann zufrieden zurückblickt: „Das Projekt hat Spaß gemacht“, sagt er. „Wenn aus dem Lehrstuhl für Theoretische Elektrotechnik am Ende etwas Praktisches herauskommt, finde ich das schön.“