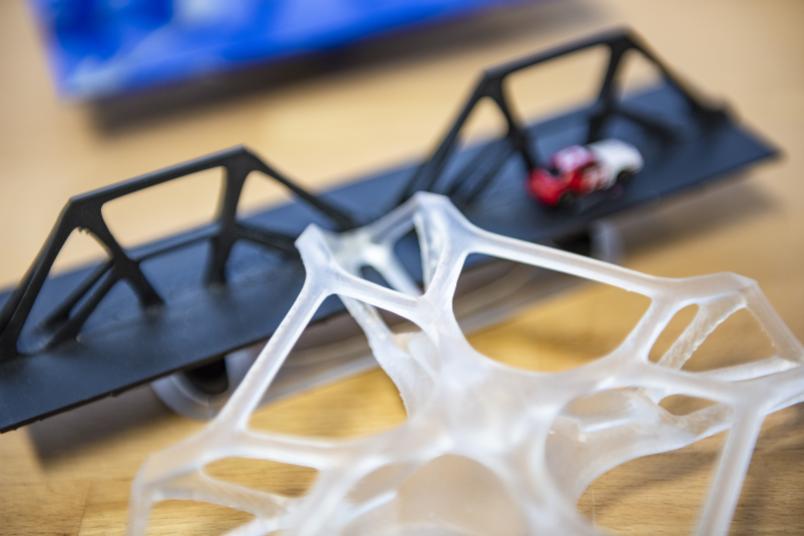
Mechanik Bauwerke und Bauteile wie natürlich gewachsen
Die Formen der durch einen Algorithmus optimierten Bauteile wirken seltsam vertraut. Das ist kein Zufall: Sie durchlaufen einen Evolutionsprozess vergleichbar zu biologischen Prozessen.
Kostengünstig, langlebig und stabil sollen Bauteile in der Regel sein. Wie man sie gestaltet, wissen Ingenieurinnen und Ingenieure aus Erfahrung. Aber könnten sie nicht noch ein wenig besser werden?
Dr. Philipp Junker vom Lehrstuhl für Kontinuumsmechanik und Dr. Dustin Jantos vom Lehrstuhl für Mechanik – Materialtheorie der RUB nutzen für die Beantwortung dieser Frage einen Algorithmus, den sie für die sogenannte Topologieoptimierung entwickelt haben. Sie geben einen Raum vor, in dem das zu planende Bauteil, zum Beispiel eine Brücke, entstehen soll. Ebenfalls vorgegeben werden die Stellen, an denen diese Brücke später befestigt werden muss. Dann lassen sie virtuell die Kräfte auf das Bauteil wirken, die auch in der Realität zu erwarten sind, im Falle der Brücke zum Beispiel Windlast und die Belastung durch den rollenden Verkehr. Durch die Berechnung schält sich dann die Brücke aus dem Raum heraus. „Das ist eine Art evolutionärer Prozess“, sagt Philipp Junker. Wo besonders große Drücke aufgefangen werden müssen, bleibt die Struktur dicker. Wo weniger starke Kräfte wirken, kann sie dünner bleiben, was Material spart.
Formen erinnern an Knochen oder Pflanzen
„Interessant ist, dass sich dabei natürlich anmutende Formen herausbilden, die zum Beispiel an Knochen oder Pflanzenteile erinnern“, sagt der Forscher. Die Stütze einer so berechneten Brücke sieht zum Beispiel sehr nach einem Baumstamm aus. Im 3D-Drucker lassen Junker und Jantos die berechneten Bauteile als reales Modell entstehen. „Man weiß vor der Berechnung nicht, welche Form dabei herauskommen wird“, sagt Dustin Jantos. „Aber die Formen, die herauskommen, sind immer nachvollziehbar.“ Sie sind häufig gar nicht so weit entfernt von bewährten Ingenieurskonstruktionen wie etwa dem Fachwerk von stählernen Eisenbahnbrücken. „Die Brückenbauer freuen sich dann natürlich, weil sie sich durch die Berechnung in ihrer Arbeit bestätigt sehen“, so die Forscher.
Eine Besonderheit des Algorithmus ist, dass die Berechnungsmethode auch komplexe Materialeigenschaften mit in die Simulation einbeziehen kann. „Man möchte natürlich kostengünstig bauen, und da Beton billiger ist als beispielsweise Stahl, möchte man ihn bevorzugt einsetzen“, erklärt Dustin Jantos. Beton weist eine hohe Stabilität gegenüber Drücken auf. Zugbelastungen kann er aber weniger gut standhalten. Teile eines Bauwerks, die solche Zuglasten tragen müssen, sollten daher eher aus Stahl gefertigt werden, oder der Beton muss stahlverstärkt werden.
Der Algorithmus kann helfen, die Verhältnisse verschiedener Materialien und ihre jeweils genutzte Menge optimal auszutarieren. Dabei bezieht die Berechnung vielfältige Eigenschaften von Materialien ein. Während sich Stahl zum Beispiel unter Belastung aus allen Richtungen gleich verhält, hält Holz bei einer Belastung in Wachstumsrichtung andere Kräfte aus als in andere Richtungen. Die Ausrichtung solcher richtungsabhängigen Materialien und auch weitere Materialeigenschaften können ebenfalls durch den Algorithmus optimiert werden.
Vorgaben und Freiheiten
Die Wissenschaftler können für die Berechnung neben dem Bauraum und den Befestigungsstellen des zu berechnenden Bauteils auch weitere Vorgaben machen, zum Beispiel zur Geometrie einzelner Teile. „Manchmal ist das wichtig, damit der Algorithmus keine Luftschlösser berechnet“, so Philipp Junker. Sonst kann es passieren, dass für eine Brücke unmöglich dünne Stahlseile berechnet werden oder für andere Bauteile Strukturen, die sich einfach nicht herstellen lassen oder aus anderen Gründen eine feste Größe haben müssen.
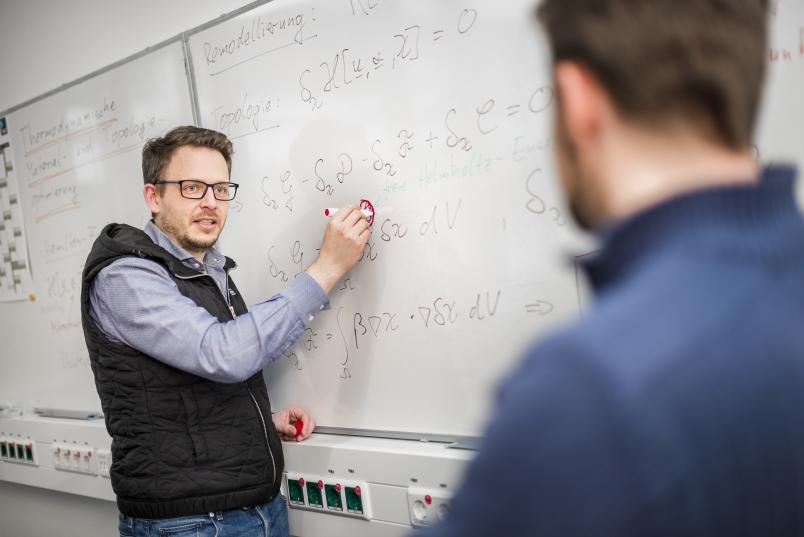
In Kooperation mit einem Industriepartner berechneten die Forscher zum Beispiel eine Kette aus Laschen und Bolzen, die ein Zahnrad antreibt. Damit die Kette zum Zahnrad passt, müssen die Bolzen einen bestimmten Durchmesser haben. Hier darf der Algorithmus also nicht ansetzen: Nur die Laschen der Kette stehen für eine Optimierung zur Verfügung. In diesem Anwendungsfall geht es darum, die Tragkraft zu maximieren oder das benötigte Material zu minimieren.
Erst 3D-Druck macht die Realisation möglich
Die Idee, per Computer mit einem an die Evolution angelehnten Verfahren Bauteile zu optimieren, ist gar nicht so neu: Schon seit 30 Jahren beschäftigen sich Forscherinnen und Forscher mit dem Prinzip. „Aber erst die Kombination mit dem 3D-Druck ermöglicht seit Kurzem die Realisierung solcher Teile“, erklärt Philipp Junker. Ohne 3D-Druck müsste man die Teile fräsen – der dafür notwendige Aufwand reduziert den Benefit der Optimierung drastisch. Da 3D-Druck auch mit Metallen durch punktuelles Aufschweißen möglich ist, vergrößert sich die Palette der Bauteile, die auf diese Weise hergestellt werden können. Ganz neu hinzugekommen zur Berechnung ist die Einbeziehung der Materialeigenschaften, wodurch nun das Zusammenspiel aus Geometrie und Material im finalen Bauteil optimiert wird und ganz neue Designformen entstehen. „Das ist unsere Spezialität“, sagt er.