Tunnelbau
Gegen Furchen, Risse und Materialbruch
Wer den Verschleiß unterirdischer Tunnelbaufabriken besser versteht, kann ihn hinauszögern und den Tunnelbau effizienter gestalten.
Wenn ein neuer Tunnel gebaut werden soll, stehen die Bauherren vor einem Dilemma: Damit der Bau kostengünstig ist, sollte er möglichst schnell gehen. Je schneller sich aber eine Tunnelbaumaschine durch die Erde bohrt, desto mehr werden die Werkzeuge belastet und verschleißen verstärkt. Das Optimum zwischen schnellem Bau und schonender Bauweise zu finden, helfen Ingenieure der RUB, die im Sonderforschungsbereich 837 an vielen verschiedenen Aspekten des Tunnelbaus forschen.
Fahrende Fabrik unter der Erde
Arne Röttger vom Institut für Werkstoffe hat dabei besonders die Werkzeuge im Blick, die an der sogenannten Ortsbrust arbeiten. „Man muss sich vorstellen, dass sich beim Tunnelbau eine fahrende Fabrik durch das Erdreich arbeitet“, beschreibt er. An der Ortsbrust wird der anstehende Boden abgebaut. Das Schneidrad ist dabei das vordere Ende einer mitunter bis zu 200 Meter langen und bis zu 17 Meter hohen Tunnelbaumaschine. Schälmesser und Schneiddisken sind je nach Bodenbeschaffenheit auf einem Schneidrad montiert. Die einen schaufeln lockere Erdschichten weg, die anderen verursachen Risse in festem Gestein und bewirken so den Bodenabbau.
Der Bodenabtransport und die entgegengesetzten Materialströme sind eine logistische Meisterleistung.
Arne Röttger
Der Abraum wird abtransportiert, der entstehende Hohlraum direkt mit gewölbten Betonteilen, sogenannten Tübbingen, ausgekleidet und der Spalt zwischen Erdreich und Betonbefestigung mit Spritzbeton verfüllt. „Gerade der Bodenabtransport und die entgegengesetzten Materialströme der benötigten Materialien zum Tunnelausbau in Richtung der Ortsbrust sind eine logistische Meisterleistung“, sagt Arne Röttger.
„Je nachdem, wie das Erdreich beschaffen ist, verschleißen die Werkzeuge an der Ortsbrust unterschiedlich schnell und in unterschiedlicher Art und Weise“, erklärt er. Weichere Metallteile zum Beispiel werden von harten Bodenbestandteilen geritzt oder gepflügt. In harten Werkstoffen bilden sich Risse, die sich bei anhaltender Belastung ausbreiten und zum sogenannten katastrophalen Versagen führen können: zum Bruch des ganzen Werkstücks. Um solch einen Bruch zu vermeiden, ist es auch wichtig, zu wissen, ob und wo sich Findlinge im Boden befinden. Diese großen Steine können die Abbauwerkzeuge durch schlagende Beanspruchung zerstören. Um sie vorab zu finden, erkunden die Ingenieure und Geowissenschaftler den Baugrund, bevor sie mit dem Tunnelbau beginnen.
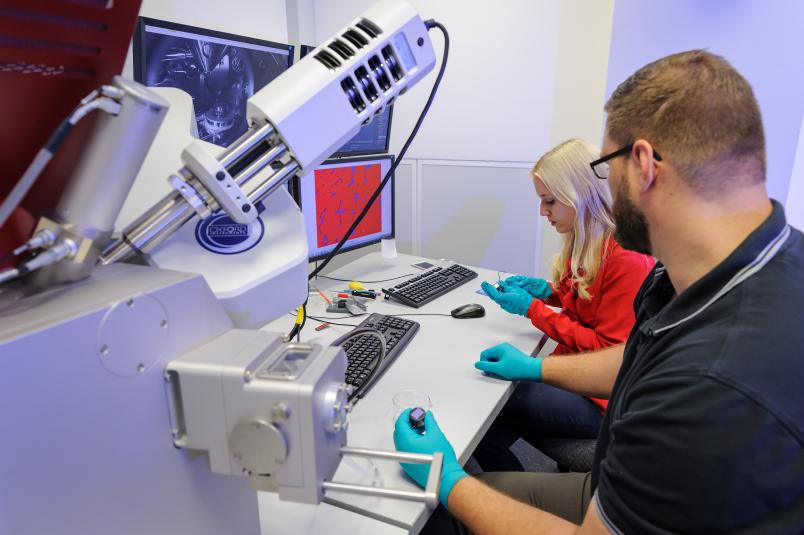
Müssen Werkzeuge an der Tunnelbaumaschine ausgetauscht werden, ist das mit viel Aufwand und daher mit hohen Kosten verbunden: Die Vortriebsmaschine muss zurückgefahren werden, Techniker müssen in den unfertigen Tunnel vor der Ortsbrust und unter gefährlichen Bedingungen teils bei Überdruck arbeiten.
„Wir versuchen deswegen, den Verschleiß solcher Werkstoffe besser zu verstehen“, sagt Arne Röttger. Das ermöglicht eine bessere Prognose des Verschleißes. „Man sieht ja nicht, in welchem Zustand die Werkzeuge sind“, erklärt Röttger. „Wir wollen gerne dahin kommen, sagen zu können, nach wie vielen Kilometern die Abbauwerkzeuge jeweils gewechselt werden müssen, damit sie nicht prophylaktisch zu früh, aber auch nicht erst bei Leistungsverlust der Maschine ausgetauscht werden.“ Darüber hinaus entwickeln die Ingenieure optimierte Werkstoffe für unterschiedliche Beanspruchungen.
Die Erde wirkt auf das Werkzeug zurück
Grundlegend dafür ist die Vorstellung, dass nicht nur die Vortriebsmaschine auf die Erde einwirkt, sondern dass die Erde auch zurückwirkt, und weitere Faktoren Einfluss auf das Ganze nehmen, zum Beispiel die Geschwindigkeit des Tunnelvortriebs, die Eigenschaften des Bodens oder zusätzliche Stoffe, die als sogenannte Konditionierungsmedien in den Boden eingebracht werden, um ihn günstig zu beeinflussen. Dieses Zusammenspiel bezeichnen die Forscher als tribologisches System. Röttger und seine Kolleginnen und Kollegen erarbeiten maßgeschneiderte Werkstoffe für verschiedenste Beanspruchungen.
Zusammensetzung und Geometrie der Werkzeuge anpassen
Dabei geht es zum Beispiel darum, die Zusammensetzung der Werkstoffe, aber auch deren Geometrie besser anzupassen, um sowohl den Abbauprozess zu optimieren als auch den Werkzeugverschleiß zu mindern. „Die meisten Werkzeuge für Lockergestein sind Werkstoffverbunde“, erklärt Arne Röttger. „Das Substrat ist ein hochfester Stahl. Aufgeschweißt oder eingelötet werden lokale Panzerungen, die solche Stellen verstärken, an denen die Belastung besonders groß ist.“ Für einen zusätzlichen Verschleißschutz werden sogenannte Hartlegierungen, Hartverbundwerkstoffe oder Hartmetalle mit teils keramikähnlichen Eigenschaften eingearbeitet.
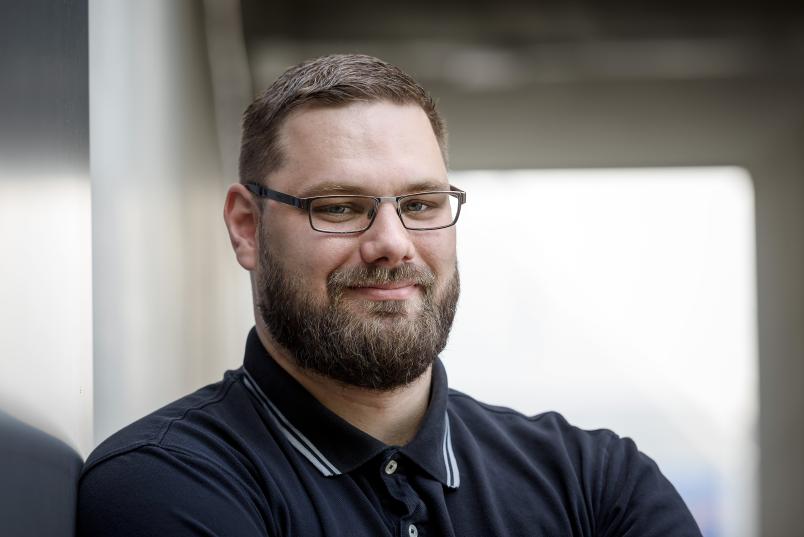
Wichtig ist dabei das richtige Gleichgewicht: Je härter ein Material, desto spröder, also anfälliger für Risse ist es. Weichere Materialien sind zwar nicht so widerstandsfähig gegen das Ritzen durch hartes Gestein, dafür aber zäher und brechen nicht so leicht. Die Beschaffenheit der Werkstoffe lässt sich außerdem durch das Herstellungsverfahren und durch eine Wärmebehandlung beeinflussen. „Speziell durch die Wärmebehandlung können wir die Mikrostruktur des Materials und die damit verbundenen Eigenschaften wie Materialhärte und Zähigkeit gezielt einstellen“, erklärt Arne Röttger.
Werkstoffe gezielt designen
Um verschiedene Werkstoffe experimentell zu prüfen, haben die Forscher im Labor einen Versuchsaufbau, bei dem ein Diamantindenter die zu prüfende Materialoberfläche ritzt. „Unter dem Elektronenmikroskop kann man deutlich erkennen, dass der Diamantindenter das weichere Metall ritzt, hingegen durch die harten, keramikähnlichen Gefügebestandteile aus dem Verbundgefüge herausgehoben wird“, so Arne Röttger.
Je nachdem, welche Eigenschaften der Boden hat, durch die die Maschine fahren soll, wählt man den entsprechenden Werkstoff aus, der sich ihm möglichst lange entgegensetzen kann. „So kann man den Werkstoff an den jeweils dominierenden Schädigungsmechanismus anpassen, also gezielt designen“, erklärt Röttger.