Bauforschung
Bis die Verbundstütze bricht
Neue Verbundkonstruktionen und Hochleistungswerkstoffe versprechen Vorteile für den Bau. Ihre Sicherheit müssen sie unter extremen Bedingungen in der Versuchshalle beweisen.
Schlankere Konstruktionen, mehr Nutzfläche und besserer Brandschutz: Neue, hochfeste Verbundkonstruktionen mit Hochleistungswerkstoffen versprechen Verbesserungen für den Bau. Noch sind sie nicht im Einsatz, weil es für sie keine Erfahrung in der Praxis und keine Normung gibt. Ihre Eigenschaften müssen zunächst gründlich geprüft werden, vor allem ihre Sicherheit. Damit beschäftigen sich Ingenieure wie Przemyslaw Schurgacz und Dennis Witteck.
In der Doktorarbeit von Przemyslaw Schurgacz stehen Stützen im Mittelpunkt, die zum Beispiel beim Bau von Hochhäusern zum Einsatz kommen. Anders als übliche Verbundstützen, die beispielsweise aus einem mit herkömmlichem Beton gefüllten Stahlrohr bestehen, hat er die Eigenschaften zweier verschiedener Konstruktionen geprüft: Zum einen ein betongefülltes Hohlprofil aus höchstfestem Stahl, in dessen Innern ein massiver Stahlkern liegt. Zum anderen eine Stütze, in deren Innern ein weiteres Stahlrohr liegt, das wiederum mit Hochleistungsbeton gefüllt ist.
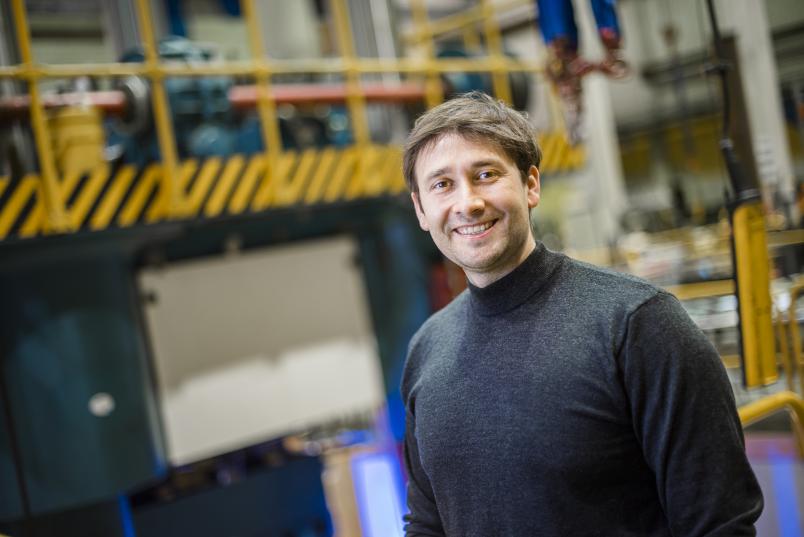
„Alle Werkstoffe haben ihre Charakteristika, die Vor- und Nachteile mitbringen“, sagt Schurgacz. So ist Beton ein verhältnismäßig günstiger Baustoff, der außerdem über gute isolierende Eigenschaften gegenüber Temperaturen verfügt. Das verzögert im Brandfall die Erwärmung. Allerdings ist er massig, oftmals nur ungenau zu verarbeiten und sieht nach einiger Zeit bisweilen nicht mehr schön aus. Stahl hingegen erlaubt schlankere Konstruktionen und ist sehr präzise und schnell montierbar. Dafür erwärmt er sich schnell und erfordert im Brandfall oft zusätzliche (Schutz-)Maßnahmen.
Mehr als 2.000 Tonnen drücken auf die Stütze
Die beiden geprüften Konstruktionen sollen die guten Eigenschaften beider Werkstoffe vereinen. Der hochfeste Spezialbeton im Innern der Stützen entsteht durch die Wahl sehr feiner Sande und chemischer Zusätze.
Um herauszufinden, was die Stützen unter realistischen Bedingungen aushalten, fertigte das Team des Lehrstuhls für Stahl-, Leicht- und Verbundbau von Prof. Dr. Markus Knobloch die ein- und zweigeschossigen Verbundstützen in der Gemeinschaftseinrichtung Konstruktionsteilprüfung KIBKON der Fakultät Bau- und Umweltingenieurwissenschaften und betonierte sie in einem Fertigteilwerk. Die Stützen wurden dann in der Halle der Konstruktionsteilprüfung in die große Prüfmaschine eingebaut und geprüft. Die Maschine ist eine der weltweit größten ihrer Art und besitzt eine Kapazität von 2.000 Tonnen – das entspricht mehr als 2.000 VW Käfer. „Die Anlage fängt schon im Keller an“, schildert Przemyslaw Schurgacz. „Anders hätten wir die über acht Meter langen Stützen der zweigeschossigen Ausführung nicht testen können.“
Für die Prüfung dieser Stützen kam erstmals ein neues optisches Messystem zum Einsatz. Es erfasst mittels mehrerer Kameras Verschiebungen der Stützen im dreidimensionalen Raum. Dafür wurde die gesamte Prüfmaschine mit Punktmarkern versehen. „Die dazugehörige Software vergleicht die Position der Marker auf jeder Aufnahme und kann so die geringsten Abweichungen und Bewegungen registrieren“, erläutert Dennis Witteck.
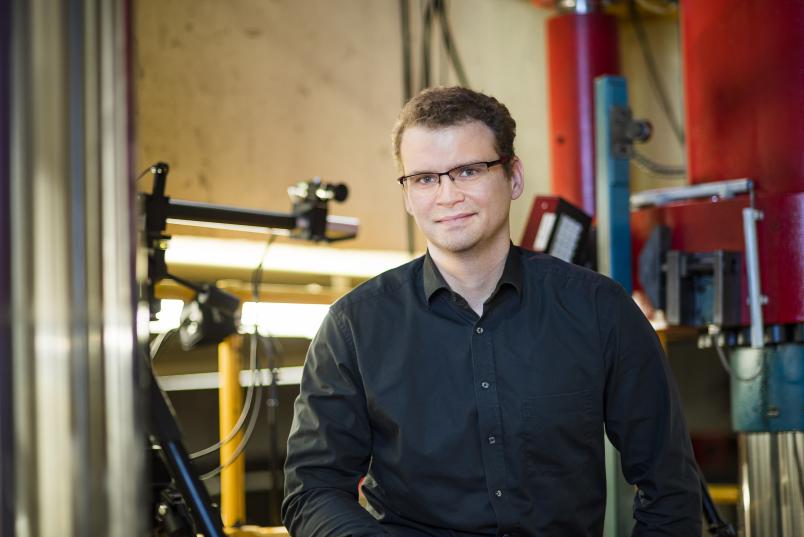
Im eigentlichen Versuch nutzten die Forscher dann die Möglichkeiten der Prüfmaschine aus und ließen eine Druckkraft von bis zu 2.000 Tonnen auf die Stütze wirken. So war es weltweit zum ersten Mal möglich, solche Verbundstützen unter realistischen Bedingungen, wie sie in Hochhäusern und anderen Megastrukturen vorherrschen, zu testen. Die Stützen hielten der Belastung zunächst lange stand, bevor sie sich zur Seite durchbogen und so einer weiteren Lastaufnahme entzogen.
Hunderte Hochhäuser sind in Planung
Die Versuchsergebnisse zeigen, dass die Verwendung von Hochleistungswerkstoffen vor allem für eingeschossige Verbundstützen großes Potenzial besitzt. „Der Einsatz der neuen Werkstoffe ist nur bis zu einer bestimmten Länge der Stütze zielführend und wirtschaftlich“, so Przemyslaw Schurgacz. „Allerdings ist für derartige Verbundstützen gerade die kürzere eingeschossige Ausführung das größte Anwendungsgebiet.“ Mit Blick auf die in europäischen und weltweiten Großstädten geplanten Hochhäuser ergebe sich für die nächsten Jahre ein großes Marktpotenzial für die innovativen Verbundstützen. Allein für London und Frankfurt sind in den kommenden Jahren schätzungsweise 250 beziehungsweise 200 Hochhäuser geplant.
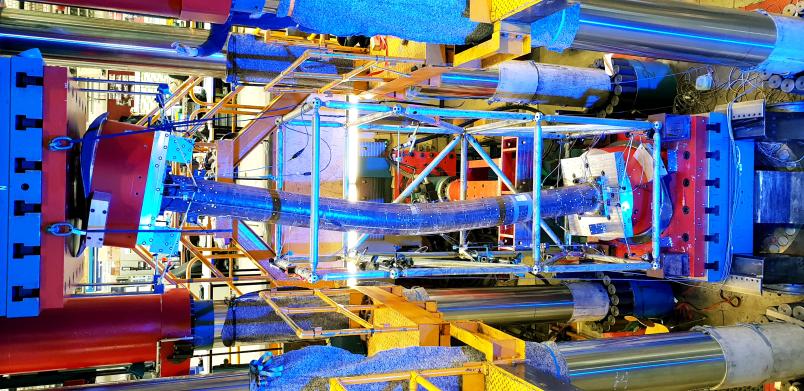
Dennis Witteck konzentriert sich in seiner Arbeit nicht auf den Normalfall der Bemessung der Verbundstützen für Einwirkungen wie Wind und Schnee, sondern auf eine außergewöhnliche Gefahr: Ihn interessiert, wie sich diese Verbundkonstruktionen aus Hochleistungswerkstoffen bei Erdbeben bewähren. „Man hat bei einem schweren Erdbeben 1995 in Kobe in Japan festgestellt, dass konventionelle Verbundstützen, die aus einem mit Beton gefüllten Rohr bestehen, der Belastung bestens standgehalten haben. Sie besitzen sehr gute Dämpfungseigenschaften und Duktilität“, berichtet er. Nun ist die Frage, ob das auch für Konstruktionen aus höherfesten Stählen und Betonen gilt. Normalerweise bringt eine erhöhte Festigkeit auch eine größere Sprödigkeit mit sich, die im Erdbebenfall ungünstig ist.
Bei einem Erdbeben muss ein Kollaps einzelner Stockwerke durch das Versagen von Stützen vermieden werden. Um Konzepte und Strategien dazu zu prüfen, entwickelte das RUB-Team einen eigenen Versuchsaufbau in der großen Prüfmaschine. Neben Druckkräften werden auf die Stütze horizontale Verschiebungen aufgebracht, die die Bewegungen eines Erdbebens nachahmen. Für die Messung wird in diesen Versuchen neben Punktmarkierungen die Oberfläche der Stütze gesprenkelt, um die Beanspruchungen des Bauteils sichtbar zu machen. Die Software des Kamerasystems erfasst so gestauchte Bereiche in rot und Bereiche, die gedehnt werden, in blau.
Die ersten Versuche und numerischen Simulationen lieferten vielversprechende Ergebnisse für den Einsatz dieser Verbundstützen in seismisch aktiven Regionen wie Südeuropa, Japan und Kalifornien. „Die innovativen Verbundstützen mit hochfesten Materialien sind eine wirtschaftlich sinnvolle Lösung für den Geschossbau, weil sie große Lasten abtragen, weil kleine Stützenquerschnitte möglich sind und hohe Brandschutzanforderungen erfüllt werden können“, fasst Dennis Witteck die Ergebnisse zusammen. Die Hauptversuchsserie läuft zurzeit. Mit den Ergebnissen rechnen die Ingenieure im Laufe des Jahres 2021.