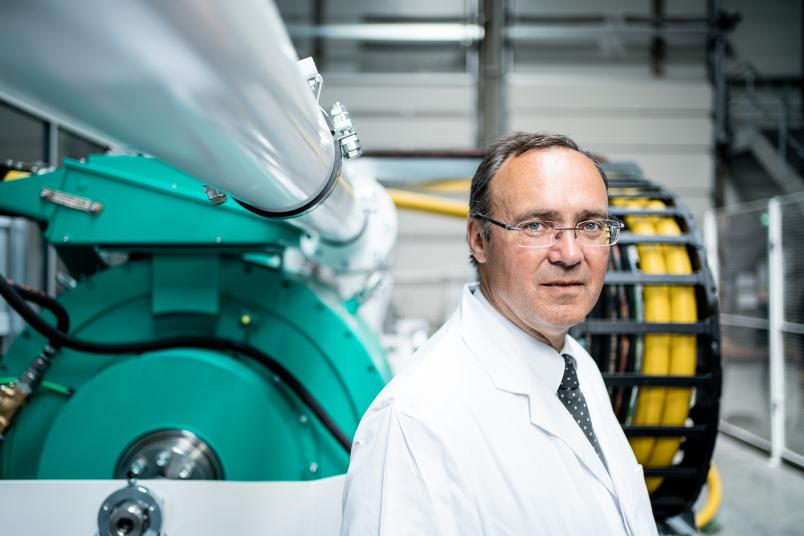
Maschinenbau
Das Wasser die Arbeit machen lassen
Für viele Techniken muss man tief in die Erde bohren, zum Beispiel für die Geothermie. Bislang genutzte Bohrverfahren bleiben dabei noch weit hinter ihren Möglichkeiten zurück.
Wasser, Hitze und mechanische Kräfte macht sich das Team von Prof. Dr. Rolf Bracke zunutze, um neue Bohrverfahren zu entwickeln, die auch unter den extremen Bedingungen tief unter der Erdoberfläche funktionieren. Die Forschung findet an der Schnittstelle zwischen Ingenieur-, Geo- und Materialwissenschaft statt. Rolf Bracke wurde 2020 auf den Lehrstuhl für Geothermische Energiesysteme an der RUB berufen und ist zudem Leiter der Fraunhofer-Einrichtung für Energieinfrastrukturen und Geothermie, kurz IEG, die Anfang 2020 ihre Arbeit in Bochum aufgenommen hat. Im Interview erzählt er, wie neue Bohrverfahren entwickelt werden, wie sie funktionieren und welchen Nutzen sie haben könnten.
Herr Professor Bracke, Sie erforschen verschiedene Bohrverfahren, mit denen man tief in die Erdkruste eindringen kann. Für welche Zwecke braucht man solche Bohrungen?
Interessant sind sie zum Beispiel im Kontext der Energiewende. Wir wollen weg von Erdöl und Erdgas hin zu einem Kohlenwasserstoff-freien Energiesystem, zum Beispiel mithilfe der Geothermie. Dafür muss man vier bis fünf Kilometer tief in die Erdkruste bohren. Tiefe Bohrungen benötigt man aber auch für die Atommüll-Endlagersuche oder für Erkundungsbohrungen im Bergbau oder für den Bau von Tunnelsystemen. Es gilt immer noch der alte Bergmannsspruch: Vor der Hacke ist es düster. In den Untergrund können wir nur reingucken, wenn wir ihn mit geeigneten geophysikalischen Verfahren untersuchen oder reinbohren.
Was sind die Herausforderungen bei diesen Bohrungen?
Auf dem Weg in die Tiefe trifft man sehr verschiedene Gesteine an. Diese Gesteine sollen unter teilweise extremen temperatur-, druck- und gesteinsspezifischen Randbedingungen möglichst schnell und einfach zerstört werden. Das zerstörte Gestein muss dann aus einigen Kilometern Tiefe an die Oberfläche transportiert werden.
Und welche Verfahren eignen sich dafür?
Traditionell bohrt man mechanisch mit Meißeln, die sich teilweise gegeneinander drehen und das Gestein abschaben. Das macht man seit 100 Jahren so, die Branche ist relativ konservativ. Allerdings arbeitet sich das Werkzeug an dem Gestein ab, es gibt einen hohen Verschleiß. Aus der Wissenschaft heraus versuchen wir daher, ein Arbeitsmedium zu finden, was das Gestein leichter zerstört. Man kann nicht nur mechanisch bohren, sondern auch thermisch oder hydraulisch oder mit einer Kombination davon.
Mit Hitze und Wasser lässt sich das Gestein zerstören?
Welches Verfahren sich eignet, hängt immer vom Gesteinstyp ab. Wenn man Wasser fokussiert und unter einen hohen Druck von 1.000 bar und mehr setzt, wird es härter als das Gestein. Man kann auch Metall mit Wasser schneiden, dafür gibt es bereits etablierte Verfahren. Wir entwickeln nun Bohrköpfe und hydraulische Systeme, mit denen man über Entfernungen von mehreren Kilometern bohren kann. Wir nutzen das Wasser zum einen, um das Gestein aufzulösen, zum anderen, um das zerstörte Gestein an die Oberfläche zu transportieren.
Unser Prototyp kann extrem harte Gesteine zerstören.
Mit dem Lehrstuhl für Laseranwendungstechnik haben wir auch mal ein teilweise thermisches Verfahren entwickelt, bei dem wir das Gestein mit der Hitze eines Lasers vorerweichen, bevor es mechanisch abgetragen wird. Auch in diesem Verfahren benötigen wir Wasser: Das Laserlicht wird durch einen Druckwasserstrahl geleitet, damit es nicht streut, sondern fokussiert auf das Gestein trifft. In der Tiefe, wo das Gestein zerstört wird, tobt ein Dreck-Tornado. Daher nutzen wir noch einen zweiten rotierenden Wasserstrahl, der das Bohrloch im unmittelbaren Umfeld des Leitstrahls sauber hält. Unser Prototyp kann extrem harte Gesteine zerstören, die man mechanisch kaum schneiden kann, etwa Glas oder Quarzite.
In einem weiteren Verfahren mischen wir dem Wasserstrahl abrasive Stoffe bei, zum Beispiel feinste Silikatkörner, sodass eine Kombination von hydraulischem und mechanischem Abtrag entsteht. Das ist für nicht ganz so harte Gesteine geeignet.
Unsere neueste Entwicklung sind extrem schnell laufende Mikro-Bohrturbinen, die wie überdimensionale Zahnarztbohrer mit 100.000 Umdrehungen pro Minute das Hartgestein zerstören und in großer Tiefe noch aus bestehenden Tiefbohrungen heraus steuerbar sind.
Wie entwickelt man solche Verfahren?
In mehreren Stufen: Zuerst entwickeln und simulieren wir die Werkzeuge am Computer. Dann bauen wir sie in kleinem Maßstab auf und testen sie im Labor. Anschließend prüfen wir die Werkzeuge im Technikum unter ähnlichen Bedingungen, wie sie in der Erdkruste herrschen. Schließlich gehen wir damit in ein echtes Bohrloch. Wir betreiben eine Forschungsbohranlage auf dem Kalwes, mit der wir bis zu 1.000 Meter tief in die Erde bohren und die Werkzeuge unter realistischen Bedingungen testen können. Danach kommt dann der Schritt zu Großbohranlagen der Industrie.
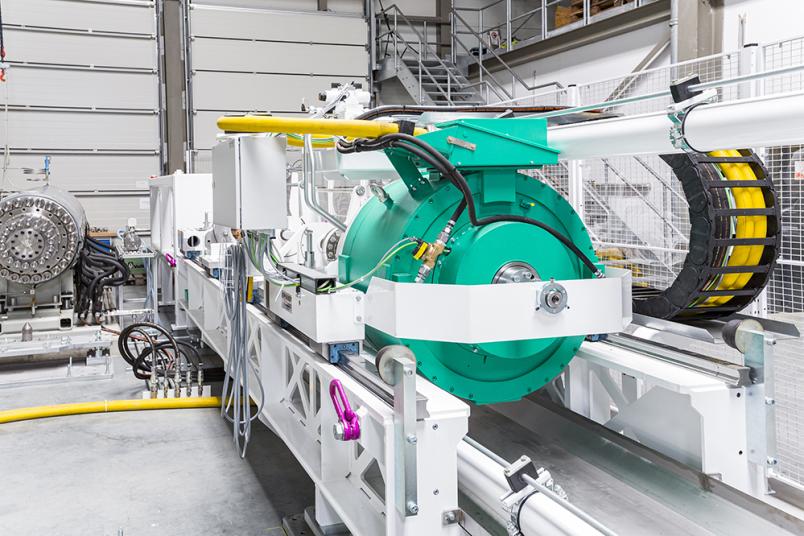
Wie lassen sich denn im Labor die Bedingungen nachstellen, die tief in der Erde herrschen?
Mithilfe unserer MATCH.BOGS, das ist ein großer Bohrlochsimulator. Die Anlage erzeugt in einem Autoklaven Temperaturen von bis zu 180 Grad Celsius und Umgebungsdrücke von über 1.000 bar. Wenn wir einen drei Meter langen Gesteinskern in den Autoklaven legen, ist es so, als ob wir ihn sechs Kilometer in die Tiefe versenken würden. Dann ist das Material nicht mehr spröde wie an der Oberfläche, sondern fängt an, plastisch zu werden. Ein Bohrwerkzeug muss in der Tiefe also quasi mit einem anderen Gestein umgehen, als wenn es an der Oberfläche arbeitet. An diesen Druckreaktor können wir eine Bohrlafette anschließen und dann unter den Bedingungen, wie sie tief in der Erde herrschen, die Interaktion von dem Bohrkopf und dem Gestein untersuchen.
Welchen Vorteil hätten solche neuen Verfahren im Gegensatz zu den etablierten?
Die Verfahren könnten schneller, sicherer und günstiger sein. Indem wir den Kontakt vom Bohrkopf zum Gestein minimieren, weil wir beispielsweise das Wasser die Arbeit machen lassen, wird der Verschleiß der Werkzeuge geringer.
Das Ziel ist, reagieren zu können, bevor das Bohrwerkzeug einen Schaden erleidet.
Außerdem arbeiten wir daran, mit akustischem Monitoring Schäden im Bohrsystem vorhersagen zu können. Wir nehmen die vielen verschiedenen Frequenzen auf, die wir während des Bohrprozesses hören. Wenn das Werkzeug erste Ermüdungserscheinungen zeigt, ändern sich die Geräusche. Die Daten werten wir mittels künstlicher Intelligenz aus. Das Ziel ist, reagieren zu können, bevor das Bohrwerkzeug tief unten in der Bohrung einen Schaden erleidet. Wenn ein kaputtes Werkzeug nicht mehr geborgen werden kann, kann das dazu führen, dass man die Bohrung aufgeben muss, die vielleicht schon einige Millionen Euro gekostet hat.
Mit ähnlichen Verfahren wollen wir den Bohrprozess in Zukunft vorausschauend steuern. Das akustische Monitoring kann uns etwas darüber sagen, wie homo- oder heterogen das Gestein ist, das vor dem Bohrkopf liegt, oder ob ein Schichtwechsel zum Beispiel von Sandstein zu Hartgestein ansteht. Dann könnte man die Bohrparameter wie Druck oder Drehzahl entsprechend anpassen. Dazu entwickeln wir ein selbstlernendes automatisches Verfahren basierend auf Big Data und künstlicher Intelligenz.