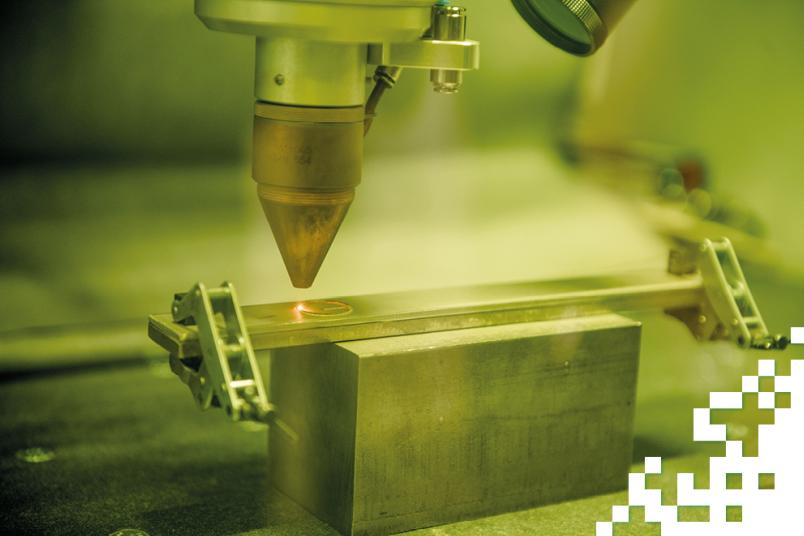
Themenwoche Digital total
3D-Druck mit Metallen
Ein Problem des herkömmlichen 3D-Drucks ist, dass er überwiegend nur Kunststoffteile erzeugt. An der RUB werden längst beliebige Strukturen aus Metallen gedruckt. Dank Lasertechnik.
Mit einem Pedal ähnlich wie bei einer Nähmaschine wird die in grünem Licht erstrahlende Anlage in Gang gesetzt. Funken sprühen, und wie aus dem Nichts entsteht ein filigraner Metallring auf einer Halterung. Nach wenigen Minuten ist er zu einem Kegel von zwei Zentimetern Höhe angewachsen.
Zugegeben, 3D-Druck ist eine etwas saloppe Umschreibung für das, was in der Hightech-Anlage vor sich geht – Experten sprechen vom Laserauftragschweißen –, doch im Prinzip passiert das Gleiche wie im herkömmlichen 3D-Drucker: Ein digitales Modell von einem beliebigen Objekt wird in eine feste dreidimensionale Struktur umgesetzt. Nur dass die herkömmlichen Geräte lediglich Plastikteile produzieren. Die Anlagen am RUB-Lehrstuhl für Laseranwendungstechnik erzeugen Metallgegenstände, deren Formen und genauen Materialzusammensetzungen kaum Grenzen gesetzt sind.
Die Technik könnte die Ersatzteilwirtschaft revolutionieren. „Wenn an einem Metallbauteil ein paar kleine Kanten abgebrochen sind, könnte man sie mit dem Verfahren einfach wieder ansetzen“, veranschaulicht Prof. Dr. Cemal Esen. Ein Bauteil, das neu mehrere Tausend Euro kosten würde, könnte so für Kosten im zweistelligen Bereich repariert werden. „Man könnte auch Ersatzteile herstellen, die nicht mehr im Handel erhältlich sind, etwa für Oldtimer“, gibt der Laserexperte ein weiteres Beispiel. Oder bei der Entwicklung neuer Bauteile zunächst verschiedene Varianten drucken und testen, welche die beste ist, bevor die Serienfertigung mit anderen Verfahren beginnt.
Laser schmelzen Metallpulver
Das Team von Cemal Esen forscht an zwei verschiedenen Metall-Druck-Verfahren. Bei beiden wird ein metallisches Pulver durch Laserstrahlung erhitzt und geschmolzen. Aus dem flüssigen Metall wird schichtweise das dreidimensionale Objekt aufgebaut, das durch ein digitales Modell vorgegeben ist.
In der einen Anlage wird das Metallpulver im Prozess kontinuierlich an genau die Stelle geschossen, an der es benötigt wird, und dort vom Laser geschmolzen. In der anderen Anlage ist das Metallpulver großflächig verteilt, und der Laser schmilzt es nur dort, wo es nötig ist. Beides hat Vorteile: Die erste Anlage verbraucht weniger Material und ist schneller, die zweite kann filigranere Strukturen herstellen, die gerade einmal 80 bis 100 Mikrometer dünn sind.
Fehler live korrigieren
„Metallgegenstände werden üblicherweise aus Vollmaterial gefräst, beim Laserauftragsschweißen ist der Materialverlust viel geringer“, erklärt Magnus Thiele, der am Lehrstuhl für Laseranwendungstechnik seine Doktorarbeit schreibt. Gemeinsam mit vielen Kollegen aus den ingenieurwissenschaftlichen Fakultäten der RUB wollen die Forscher in Cemal Esens Team den Prozess weiter optimieren, zum Beispiel schneller und stabiler machen.
„Wir wollen kleine Fehler, die im Prozess entstehen, sofort identifizieren und live korrigieren können“, erklärt Henrik Dobbelstein, ebenfalls Doktorand in der Gruppe. Dazu müssen die Forscher die Anlage zunächst mit der entsprechenden Sensorik ausstatten, die den Druck in Echtzeit überwachen kann und zuverlässige Daten für die Kontrolle liefert. Daran arbeitet das Team im Rahmen des Projekts „Itself“, das das Bundesministerium für Bildung und Forschung fördert.
Fernziel: Künstliche Intelligenz
Die Zukunftsvision: „Eines Tages sollen die Anlagen mithilfe Künstlicher Intelligenz selbst die optimalen Prozessparameter finden, zum Beispiel die Laserleistung und Geschwindigkeit selbst einstellen können“, erklärt Cemal Esen. Die Sensoren, die sein Team derzeit in die Anlagen implementiert, würden dem Gerät das dafür notwendige Feedback geben.